Customer Site
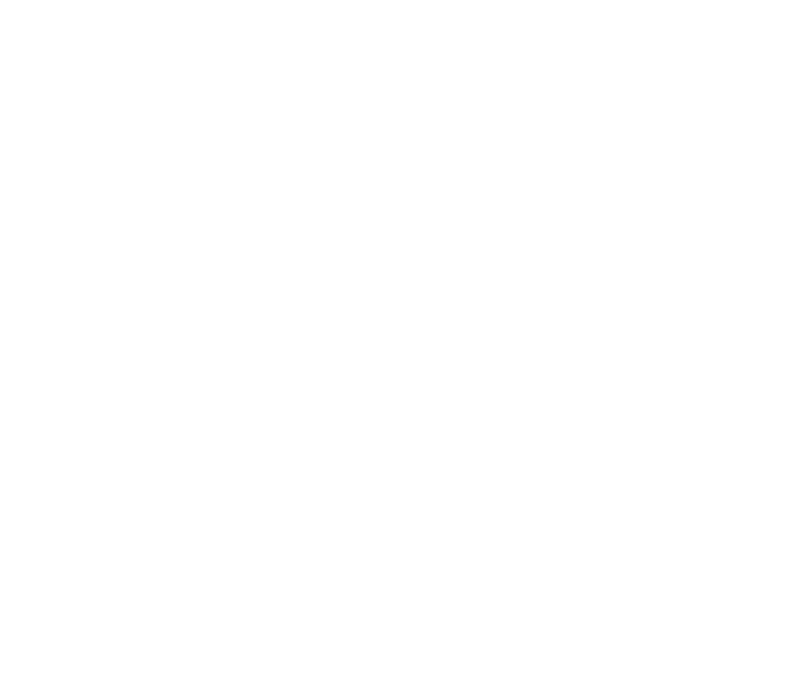
Customer Background
A large metal component manufacturer in India, specializing in steel structure production for 20 years. The company processes over 15,000 tons annually, and its products are widely used in infrastructure and industrial equipment sectors.
Transformation Challenges
- Manual welding has resulted in a daily production capacity stagnating at 35 components.
- The weld seam qualification rate is only 82%, with rework costs accounting for 6% of revenue.
- The turnover rate of skilled welders is as high as 40%, and labor costs are increasing by 18% annually.
Solution
- Introduce our intelligent rail-type welding robots.
- Dual-station collaborative operation design.
- Equipped with a laser seam tracking system.
- Supports presetting of 12 complex welding process parameters.
Implementation Results (After 6 Months of Equipment Operation)
- Efficiency Breakthrough: Single-shift production capacity increased to 120 components, with welding speed reaching 2.1 meters per minute.
- Quality Improvement: First-pass weld seam qualification rate increased to 98.7%, saving $280,000 annually in rework costs.
- Labor Optimization: Personnel demand in the welding process reduced by 60%, with annual operational costs decreasing by $150,000.
Client Testimonial
"This system revolutionized our production capacity. We're now confidently bidding on major bridge projects that were previously impossible." – Production Director